Die Druckgussproduktion trifft häufig auf die Entwicklung neuer Produkte und die Aktualisierung alter Formen. Im Allgemeinen hängt die innere und äußere Qualität von Druckgussteilen von Prozessparametern des Druckgussverfahrens ab, wie z. B. Schmelztemperatur, Druckgussdruck, Geschwindigkeit und Geschwindigkeitsschaltpunkten. In den meisten Fällen ist es aber auch eng mit der Werkzeugkonstruktion und -produktion verbunden. Zu den Faktoren, die die Form beeinflussen, gehören die Anzahl der Kavitäten, das Design des Angusssystems, die Art des Anschnitts (Position und Größe) und die Struktur des Gussstücks selbst. Um Gießfehler zu vermeiden, die durch die Formkonstruktion verursacht werden, und um einige Probleme beim Formenbau zu inspizieren und zu beheben, ist es notwendig, die fertige Form zu testen.
Druckgussformversuch und Optimierung der Prozessparameter
Der Hauptzweck des Formversuchs besteht darin, die optimierten Prozessparameter und den Formmodifikationsplan herauszufinden, und es ist erforderlich, dass selbst wenn sich die Materialien, Maschineneinstellungen oder Umgebung und andere Faktoren geändert haben, immer noch sichergestellt werden muss, dass die Form funktioniert kann stabile und ununterbrochen qualifizierte Produkte in Chargen produzieren. Maximieren Sie den "Fit" der Form, nicht nur um ein paar gute Versuche zu machen.
Finden Sie das Problem mit dem Schimmel heraus
Es wird erwartet, dass die von der Formenfabrik hergestellte Form eine Form mit guter "Anpassungsfähigkeit" ist (d. h. die Formparameter oder Prozessbedingungen sind breit gefächert). Aufgrund schlechter Designüberlegungen oder unzureichender Verarbeitung im Produktionsprozess treten jedoch häufig einige Probleme auf, wie z. kann nicht erledigt werden. Und Tryout ist der einfachste, direkteste und effektivste Weg, um das Problem der Form herauszufinden.
Finden Sie die besten Umformbedingungen
Im Formversuchsprozess kann das Formversuchspersonal einen Satz der am besten geeigneten Prozessdaten finden, und dieser Datensatz kann als Standardwert zum Einstellen von Maschinenparametern während der Massenproduktion verwendet werden, und der am besten geeignete Formmassenproduktionsprozess kann verwendet werden entsprechend diesem Datensatz angepasst werden. optimale Prozessbedingungen.
Verifizieren Sie das CAE-gestützte Design und verbessern Sie die Effizienz der Folgearbeit
Die CAE-Analysesoftware basiert auf den Spezifikationen realer Maschinen, der Leistung realer Legierungen und der realen externen Umgebung durch Computersimulation, den Ergebnissen von Simulationsberechnungen. Werkzeugkonstrukteure können entsprechend der Simulationssituation entsprechende Korrekturen an der Werkzeugkonstruktion vornehmen; die Analysedaten können direkt beim Werkzeugtest der realen Maschine als Vorgabewerte eingegeben werden und die Werkzeugprüfer können damit prüfen und analysieren, ob die Werkzeugkonstruktion mangelhaft ist. Die Fehler des Testmoduls können mit den Simulationsergebnissen verglichen und analysiert werden, um eine Grundlage für die nachfolgende Prozessparametrierung zu schaffen.
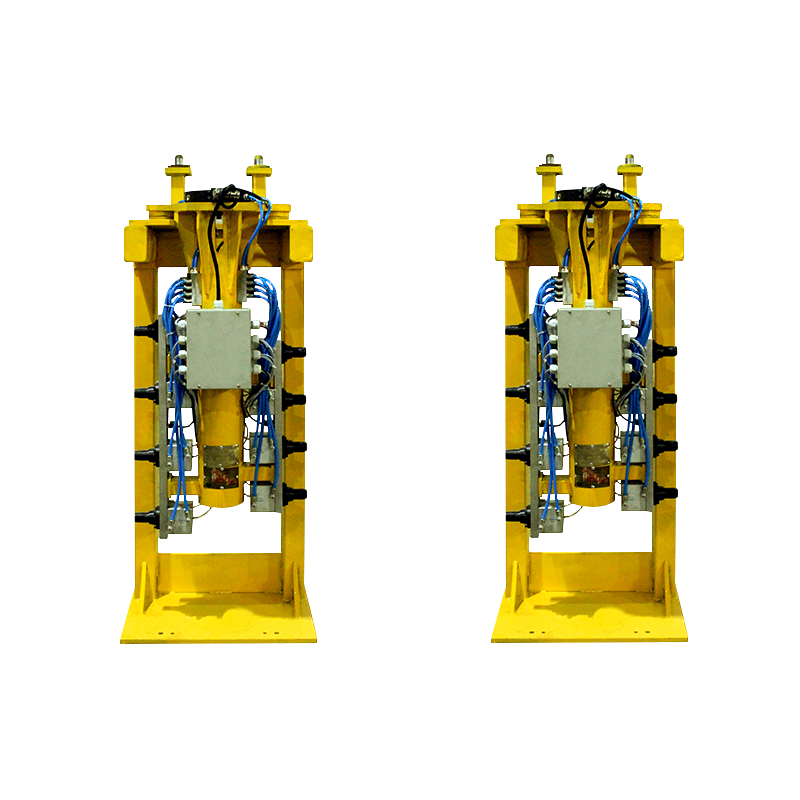