Bei der Herstellung und Verarbeitung von Druckgussformteilen gibt es aufgrund der komplexen Form und Struktur offensichtliche Unterschiede in der Querschnittsgröße jedes Teils. Wenn also eine Wärmebehandlung durchgeführt wird, sind die Erwärmungs- und Abkühlungsraten jedes Teils unterschiedlich auch anders. Diese Situation kann zur Bildung unterschiedlicher Wärmespannungen, Gewebespannungen und Phasenübergangsvolumina in verschiedenen Teilen des Teils führen. Es verursacht eine abnormale Ausdehnung oder Kontraktion des Volumens des Teils, was zu einer großen Abweichung in seiner Größe und Form und sogar zu Rissen führt.
Es gibt viele Gründe für die Wärmebehandlungsverformung und das Reißen von Druckgussformen, einschließlich der chemischen Zusammensetzung und ursprünglichen Struktur des Stahls, der strukturellen Form und Querschnittsgröße der Teile und des Wärmebehandlungsprozesses. In der realen Produktion lassen sich Verformungen oft nicht vollständig eliminieren, und das Ausmaß ihres Auftretens kann nur so weit wie möglich reduziert werden, aber solange geeignete Maßnahmen ergriffen werden, kann eine Rissbildung vollständig vermieden werden.
1. Vorbereitende Wärmebehandlung
Die sogenannte vorbereitende Wärmebehandlung ist relativ zur abschließenden Wärmebehandlung, das heißt, vor der abschließenden Wärmebehandlung wird ein vorbereitender Wärmebehandlungsschritt hinzugefügt, der eine gute Bearbeitbarkeit oder Mikrostruktur für die abschließende Wärmebehandlung bereitstellen kann. Übliche vorbereitende Wärmebehandlungsprozesse umfassen Glühen, Normalisieren, Abschrecken und Anlassen.
Bei der vorbereitenden Wärmebehandlung von eutektoiden Stahl-Stanzwerkzeugen liegt der Fokus auf der Eliminierung von retikuliertem Sekundärzementit, Kornfeinung und Eigenspannungen in Schmiedestücken. Das spezifische Verfahren besteht darin, zuerst eine Normalisierungsbehandlung durchzuführen und dann ein kugelförmiges Glühen durchzuführen. Für Stanzwerkzeuge sollte es durch Niedertemperatur-Anlassen stabilisiert werden. Bei Formen mit komplexen Formen und hohen Präzisionsanforderungen sollte aufgrund der höheren Wahrscheinlichkeit von Verformung und Rissbildung während der Wärmebehandlung eine geeignete Abschreck- und Anlassbehandlung durchgeführt werden, nachdem die Grobbearbeitung abgeschlossen ist und bevor mit der Endbearbeitung begonnen wird. Die Wärmebehandlung wird verwendet, um die Organisation vorzubereiten, um das Auftreten von Rissen so weit wie möglich zu vermeiden.
2. Abschreckende Heizmethode und Schutz der Teile
Abschrecken und Anlassen sind die Prozesse, die am anfälligsten für Verformung und Rissbildung von Teilen sind. Bei einigen kleinen Druckgussformen, schlanken zylindrischen Teilen oder Formteilen aus hochlegiertem Stahl usw. sollte das Abschreckverfahren der direkten Erwärmung vermieden werden, es sollte jedoch auf 520 bis 580 Grad Celsius vorgewärmt und dann in ein Medium gelegt werden Temperatur Salzbad Ofen. Auf Abschrecktemperatur erhitzen. Die Praxis hat bewiesen, dass die Verformung der Teile bei dieser Erwärmungsmethode deutlich geringer ist als bei direkter Erwärmung und Abschreckung in einem Elektro- oder Flammofen und Rissbildung grundsätzlich vermieden werden kann.
Wenn während des Abschreckens die Erwärmungstemperatur von austenitischen Teilen zu hoch ist, werden die Körner grob, und es ist leicht, Oxidation, Entkohlung und andere Phänomene zu verursachen, was zu Verformung und Rissbildung der Teile führt; und wenn die Temperatur zu niedrig ist, schrumpfen die inneren Löcher der Teile und die Größe der Porengröße schrumpft. werde kleiner. Versuchen Sie daher, innerhalb des zulässigen Bereichs der Erwärmungstemperatur die obere Grenze der Temperatur zum Abschrecken auszuwählen. Bei legiertem Stahl ist die Erwärmungstemperatur zu hoch, was dazu führt, dass sich das innere Loch ausdehnt und die Porengröße größer wird. Es ist am besten, die untere Grenze der zulässigen Temperatur zu wählen.
Darüber hinaus müssen beim Abschrecken und Anlassen Maßnahmen ergriffen werden, um die zu Verformung und Rissbildung neigenden Teile wirksam zu schützen, damit Form und Querschnitt symmetrisch sind und die Eigenspannung ausgeglichen ist. Dies gilt insbesondere für Teile mit komplexen Formen. Zu den häufig verwendeten Schutzmethoden gehören Ballenpressen, Füllen und Stopfen.
3. Optimierung der Kühlmethode und Auswahl des Kühlmittels
Wenn die Druckgussformteile erwärmt werden, sollten sie nach dem Herausnehmen aus dem Ofen nicht direkt in das Kühlmittel gelegt werden, da dies leicht zu einer zu großen lokalen Temperaturdifferenz und zu Verformungen und Rissen führen kann. Die richtige Methode besteht darin, die Teile zuerst an der Luft vorzukühlen und sie dann zum Abschrecken in das Kühlmittel zu legen. Um die gleichmäßige Abkühlgeschwindigkeit jedes Teils des Teils zu gewährleisten, sollte es nach dem Einfüllen des Kühlmittels ordnungsgemäß gedreht werden, und die Drehrichtung ist vorzugsweise nicht festgelegt.
Ebenso wichtig ist die Wahl des Kühlmittels. Bei legierten Stählen ist isothermes Abschrecken oder abgestuftes Abschrecken mit Kaliumnitrat- und Natriumnitrit-Heißbädern eine wirksame Methode zur Verringerung der Verformung, insbesondere bei Druckgussformen mit komplexen Formen und präzisen Abmessungen. Einige poröse Formteile haben die Eigenschaften, in Öl abzukühlen und zu schrumpfen und in Nitrat abzukühlen und sich auszudehnen. Durch den rationellen Einsatz zweier unterschiedlicher Medien kann auch die durch das Abschrecken verursachte Verformung der Teile reduziert werden.
4. Die Steuerung der Anlassbehandlung
Nach dem Abschrecken der Druckgussformteile im Kühlmittel sollten diese nicht zu lange an der Luft bleiben, sondern rechtzeitig zur Anlassbehandlung in einen Anlassofen gestellt werden, um Eigenspannungen der Teile abzubauen und die Verformungsneigung zu verringern und knacken. Insbesondere für einige Druckgussformteile, die durch Drahtschneiden, abgestuftes Abschrecken und mehrfaches Anlassen verarbeitet werden müssen, werden vor der Drahtschneidebehandlung Wärmebehandlungen verwendet, die die Härtbarkeit der Teile effektiv verbessern, die innere Spannungsverteilung gleichmäßig machen und weniger anfällig für Verformung und Rissbildung sein. Während des Anlassvorgangs ist das Auftreten von Niedertemperatur-Anlassversprödung und Hochtemperatur-Anlassversprödung zu vermeiden.
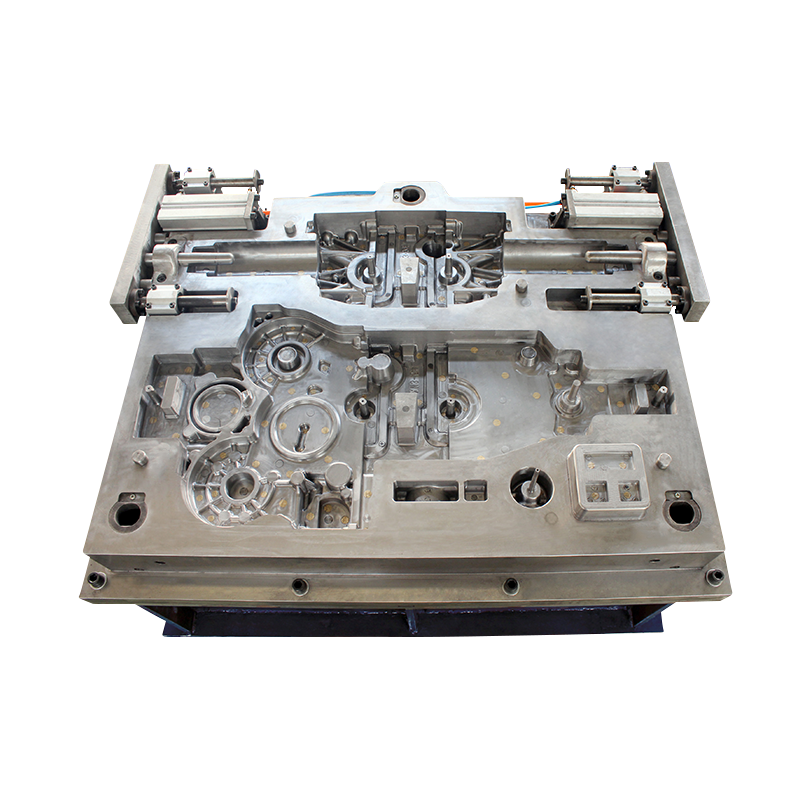